The Essential Role of an Oil Cooler Factory in the Diesel Engine Parts Industry
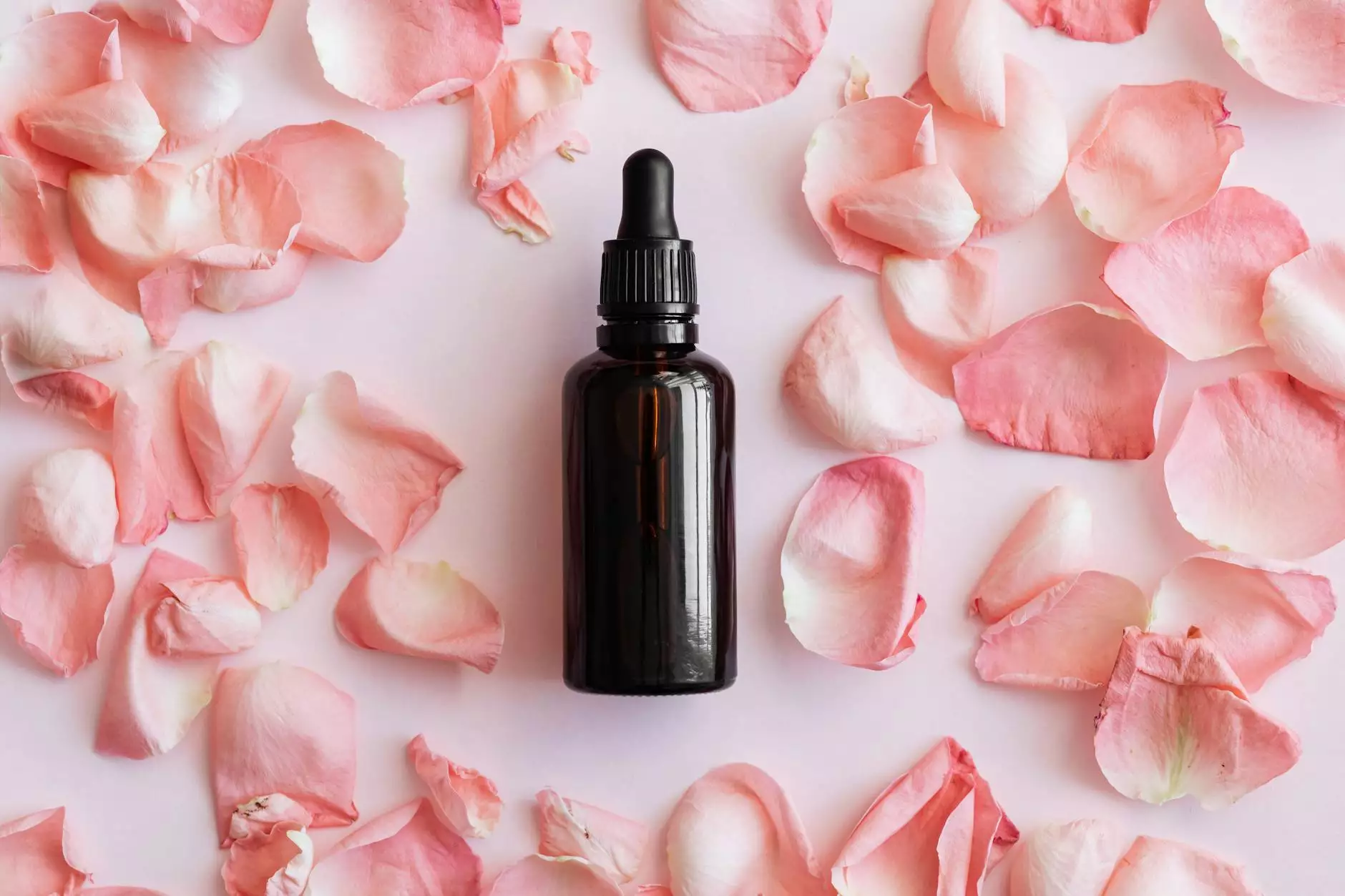
The global demand for diesel engine parts has seen a substantial increase, leading to a booming industry that requires robust, efficient manufacturing processes. In this context, the significance of an oil cooler factory cannot be understated. This article delves into the myriad aspects of oil cooler manufacturing, its impact on diesel engine performance, and the strategies businesses can employ to thrive in this competitive market.
Understanding the Importance of Oil Coolers
Oil coolers play a pivotal role in maintaining and enhancing the performance of diesel engines. They function to regulate the temperature of engine oil, which is crucial for several reasons:
- Temperature Regulation: High operating temperatures can cause engine oil to degrade rapidly, leading to increased wear and tear.
- Enhanced Engine Longevity: By maintaining optimal oil temperatures, oil coolers contribute to extended engine life and reliability.
- Efficiency Boost: Cooler oil improves fuel efficiency, resulting in cost savings for operators.
Components of an Oil Cooler and Manufacturing Process
To understand the role of an oil cooler factory, it is essential to explore the components and manufacturing processes that contribute to high-quality oil coolers.
Key Components of Oil Coolers
- Core: The core is where heat exchange takes place and is often made from aluminum or copper.
- End Tanks: These components help direct the flow of oil and are typically constructed from aluminum.
- Fins: Fins increase the surface area for heat dissipation, thereby enhancing cooling efficiency.
Manufacturing Processes in an Oil Cooler Factory
The manufacturing of oil coolers involves several critical processes to ensure product quality:
- Material Selection: Choosing the right materials is foundational to the durability and performance of oil coolers.
- Precision Fabrication: Advanced technologies such as CNC machining are used to achieve precise dimensions and specifications.
- Quality Control: Rigorous testing procedures, including pressure tests and thermal tests, ensure each cooler meets industry standards.
Market Trends and Innovations in Oil Cooler Manufacturing
The landscape of oil cooler manufacturing is continually evolving, influenced by technological advancements and market demands. Some current trends include:
Advancements in Materials
Innovative materials such as composite materials and advanced alloys are being used to manufacture lighter and more efficient oil coolers.
Integration of Smart Technology
Smart technology integration in oil coolers allows for real-time monitoring of oil temperatures, providing critical data that aids in predictive maintenance.
Challenges Faced by Oil Cooler Factories
While the prospects for oil cooler factories are promising, they also face several challenges, including:
- Regulatory Compliance: Meeting environmental and safety regulations can be a burden for manufacturers.
- Global Competition: With many players in the market, standing out requires innovation and quality assurance.
- Supply Chain Issues: Fluctuations in raw material prices and availability can impede production schedules.
Strategic Approaches for Success in the Oil Cooler Business
To succeed in the competitive landscape of the oil cooler factory market, companies must adopt strategic approaches:
Emphasizing Quality
Focusing on high manufacturing standards not only fosters customer trust but also reduces long-term costs associated with product failures.
Building Sustainable Relationships
Collaborating with reputable suppliers and forming partnerships with engine manufacturers can open new market opportunities.
Investing in Research and Development (R&D)
Continuous improvement through R&D programs leads to innovations that keep the factory ahead of industry trends.
The Certification and Validation Process
Certification is crucial for oil cooler factories, as it demonstrates product reliability and compliance with industry standards. Key certifications include:
- ISO 9001: This certification ensures quality management systems are in place, promoting consistent quality and customer satisfaction.
- ISO 14001: Focused on environmental management, this certification demonstrates corporate responsibility towards the environment.
The Future of Oil Cooler Manufacturing
Looking ahead, the future of the oil cooler factory sector appears bright. Predictions suggest increased demand due to the growth of the automotive and transportation sectors, particularly concerning diesel engines. Additionally, the push towards sustainability will likely drive innovations in manufacturing processes and materials.
Conclusion
In summary, the impact of an oil cooler factory on the performance and longevity of diesel engines is significant. As industries evolve, so too must the factories that supply critical components like oil coolers. By prioritizing quality, leveraging technology, and adapting to market trends, manufacturers can not only meet but exceed the demands of today’s market.
For more information on diesel engine parts and the intricate world of spare parts suppliers, visit client-diesel.com.