Understanding Prototype Injection Molding: Revolutionizing Metal Fabrication
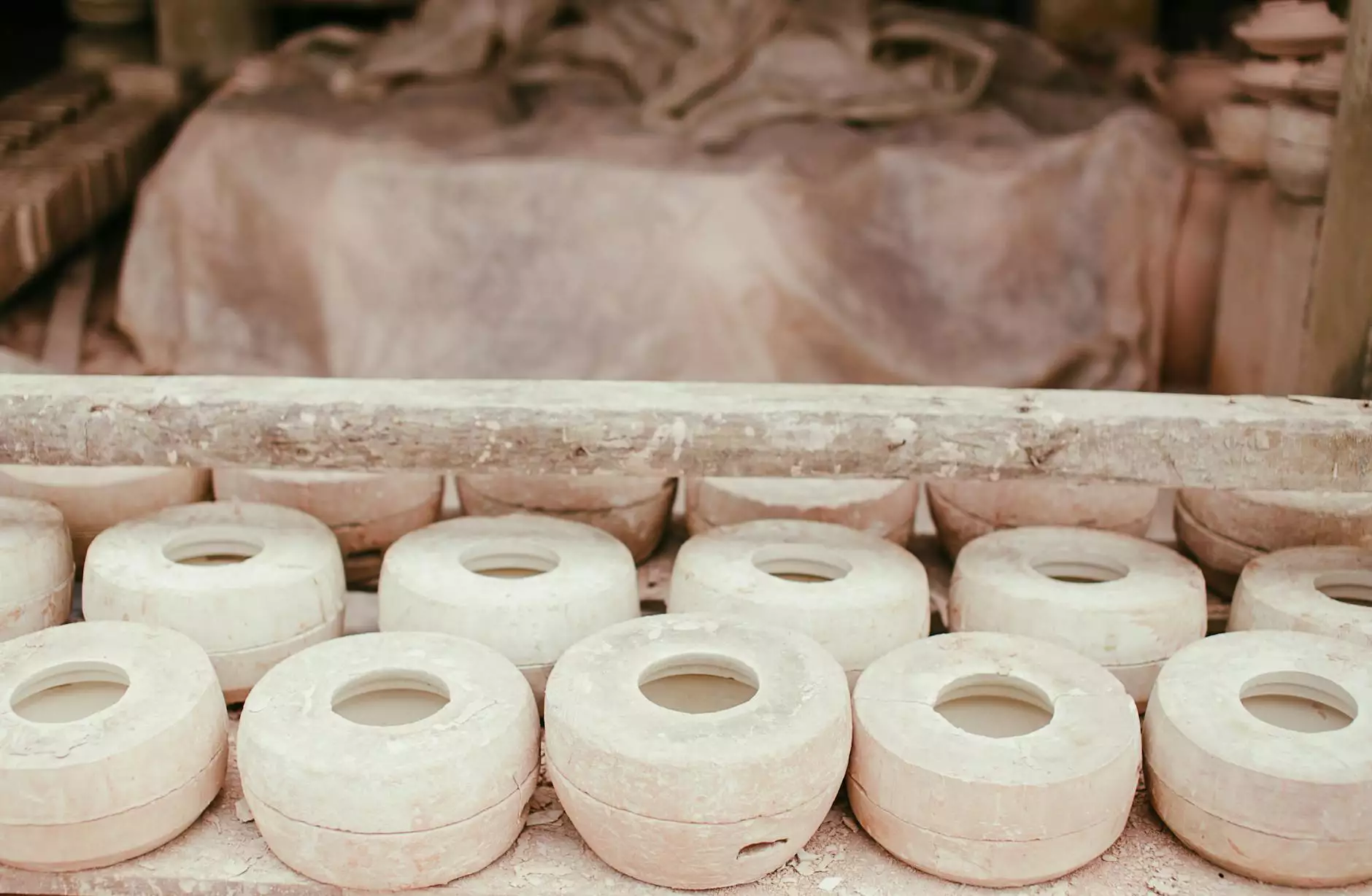
In today's competitive manufacturing landscape, prototype injection molding stands out as a crucial technique that significantly enhances product development and innovation in metal fabrication. This comprehensive guide aims to explore the nuances, advantages, and applications of prototype injection molding, particularly within the sector of metal fabrication.
What is Prototype Injection Molding?
Prototype injection molding is a manufacturing process used to produce small batches of parts from a variety of materials, including metals and plastics. This method allows for quick iterations and testing of designs before full-scale production begins.
The process involves creating a mold, which is a hollowed-out block that is filled with molten material. This material cools and solidifies within the mold, forming the desired part. The quick cycle time associated with this technique, which can be as short as a few minutes, makes it ideal for rapid prototyping and low-volume production.
Key Benefits of Prototype Injection Molding
- Cost-Effectiveness: By allowing designers to test and modify prototypes without making extensive investments, injection molding reduces overall product development costs.
- Speed: The process accelerates the prototyping phase, enabling manufacturers to bring products to market faster.
- Precision: Injection molding yields high accuracy and superior surface finishes, which are critical in metal fabrication.
- Material Versatility: This technique can work with a range of materials, providing flexibility in design and function.
- Scalability: Once the prototyping phase is successful, transitioning to mass production is seamless.
How Prototype Injection Molding Works
The prototype injection molding process consists of several key steps:
1. Design Creation
Initially, engineers create a detailed design using CAD (Computer-Aided Design) software. This step is crucial, as modifications at this stage can be cost-effective compared to later stages.
2. Mold Fabrication
Once the design is finalized, a mold is fabricated from durable materials such as steel or aluminum. The quality of the mold directly impacts the final product's accuracy and finish.
3. Material Selection
The next step involves selecting the appropriate material for injection. Factors influencing this decision include the intended use of the part, aesthetic requirements, and functional specifications.
4. Injection Process
The molten material is injected into the mold under high pressure. This ensures that all details of the design are captured. The material then cools and solidifies, taking the shape of the mold.
5. Ejection
Finally, once the part has cooled sufficiently, it is ejected from the mold. At this stage, any additional finishing processes can be applied as needed.
Applications in Metal Fabrication
Within the realm of metal fabrication, prototype injection molding has several impactful applications:
- Automotive Industry: Prototype parts are essential for testing vehicle components and improving designs before full-scale production.
- Aerospace: The aerospace sector utilizes injection molding for lightweight and durable parts that must meet stringent regulations and performance standards.
- Consumer Products: Rapid prototyping allows consumer goods manufacturers to innovate quickly, tailoring products to shifting market demands.
- Medical Devices: Precision and accuracy are paramount in the medical sector, making prototype injection molding a favoured choice for device developers.
- Electronics: The need for intricate designs in the electronics industry is met efficiently through injection molding, enabling better product functionality.
Challenges and Considerations
While prototype injection molding offers numerous advantages, it is not without its challenges:
1. Initial Setup Costs
The upfront cost to design and fabricate molds can be significant. However, these costs are often offset by long-term savings on manufacturing.
2. Design Limitations
Certain complex designs may be difficult to achieve due to mold constraints. Thus, careful design consideration is essential before proceeding.
3. Material Selection Risks
Selecting an inappropriate material can lead to production issues. It is vital to consider the properties required for the final application.
The Future of Prototype Injection Molding
As technology evolves, so does the field of prototype injection molding. Innovations in materials and methodologies are continually emerging, providing even greater capabilities and efficiencies. The integration of advanced technologies like 3D printing in the initial stages of prototyping is also reshaping the landscape, offering rapid iterations that bring concepts to life faster than ever.
Conclusion
Ultimately, prototype injection molding is not just a manufacturing process; it is a game-changer in product development within the metal fabrication industry. The seamless ability to create precise prototypes quickly and affordably allows businesses to respond to market demands with agility. Companies such as DeepMould.net are at the forefront of these advancements, offering superior solutions that leverage cutting-edge technology for optimal outcomes.
By embracing prototype injection molding, businesses can not only enhance their product offerings but also ensure they remain competitive in an ever-evolving marketplace. As industries continue to adapt and innovate, the role of prototype injection molding will undoubtedly play a crucial part in shaping the future of manufacturing.